Ford has more U.S. hourly UAW-represented workers than any other automaker and builds more vehicles in the U.S. than any other automaker. Ford is committed to a safe, harassment-free workplace for all employees. As of the end of 2018, Ford had 55,461 U.S. hourly UAW-represented workers. It is important that the company reaches a contract that keeps Ford competitive with all automakers that build in the United States. Approximately 82 percent of the vehicles Ford sells in the U.S. are built in the U.S., significantly higher than any other automaker.
National Negotiations
The current UAW-Ford national contract expires at 11:59 p.m. on Sept. 14, 2019. If a new contract is not ratified by then, the UAW and Ford can agree to extend the contract, continue working without a contract or the UAW could call for a strike.
The national contract is a series of agreements that cover the company’s UAW-represented hourly employees. These agreements generally fall into three broad categories:
- Wages and working conditions: Including base wages, paid time off, grievance procedures, management rights and general seniority matters
- Benefits: Including healthcare, retirement, supplemental unemployment benefits, profit sharing and a tax-efficient savings plan for hourly employees
- Appendices and letters of understanding : These clarify parts of agreements or deal with matters not referred to in the agreements – covering subjects such as job security, sourcing and operational effectiveness
Local Negotiations
In addition to national negotiations, Ford and the UAW will conduct local negotiations for separate hourly UAW-represented bargaining units. Most are individual plants or parts distribution centers. Each unit normally conducts its own local negotiations concurrent with the national bargaining.
U.S. Industry Sales and the Negotiations Cycle
Industry sales citations all reflect total U.S. industry, including medium and heavy trucks, which is how Ford reports industry sales. The years highlighted in blue below indicate contract talks between the UAW and Ford.
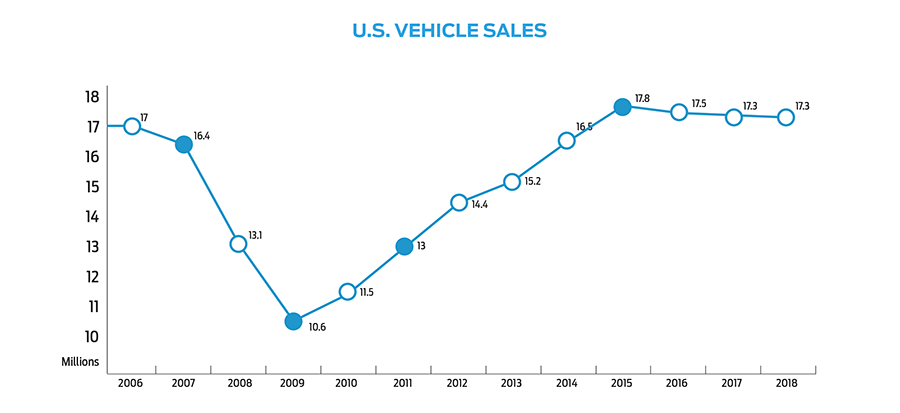
For more than a decade, Ford has been disciplined about matching production with customer demand. Volatility and disruption in the auto industry during the past 14 years has affected Ford’s business and, as a result, its negotiations and contracts with the UAW.
When Ford and the UAW negotiated in 2007, the U.S. industry was coming off an extended string of 17-million unit sales years when sales slipped to 16.4 million units, foreshadowing the severe decline that was to follow in the 2008-09 recession. In 2009, when the UAW contract was reopened for negotiation, the industry had fallen an additional 35 percent, bottoming out at 10.6 million units.
When the two sides negotiated in 2011, the industry was beginning a slow recovery, with total industry sales just clearing 13 million units that year, 25 percent below the pre-crisis peak.
By negotiations time in 2015, the industry had fully recovered and achieved a new record of annual sales topping 17.8 million units.
Since that time, the industry has plateaued, with vehicle sales leveling off at 17.5 million in 2016 and 17.3 million each of the last two years, with some economists predicting another recession in the coming years.
Ford must be ready for the next downturn, whenever it comes.
2015 UAW-Ford Contract Commitments
In the 2015 contract, Ford committed to invest $9 billion in its U.S. plants and create or retain 8,500 U.S. hourly jobs. The company exceeded those commitments.