Sep 12, 2013
Game Changer: 100th Anniversary of the Moving Assembly Line
When Henry Ford began making cars in the early 1900s, “state-of-the-art” manufacturing meant car bodies delivered by horse-drawn carriage, with teams of workers assembling automobiles atop sawhorses. The teams would rotate from one station to another, doing their part to bring the vehicle together. Parts deliveries were timed, but often ran late causing pile-ups of workers vying for space and delays in production. Fortunately for the future of industry, these archaic practices came to an end Oct. 7, 1913.
Observers of the time were already suggesting that someone needed to invent a way to mass produce cars, and by doing so bring down the price to enable more people to afford the luxury. J.J. Seaton wrote in Harper’s Weekly in January 1910 that “the man who can successfully solve this knotty question and produce a car that will be entirely sufficient mechanically, and whose price will be within the reach of millions who cannot yet afford automobiles, will not only grow rich but will be considered a public benefactor.”

Ford already had developed in 1908 the Model T, a “car for the masses.” Now it was time to find a way to make many of these cars at a rapid pace and with high quality. Ford surrounded himself with experts from various fields, such as brewing, canning and steel making, and each contributed his expertise to a solution for mass auto manufacturing. Ford’s vision and leadership enabled him to create a climate where his team could collaborate, bring new ideas and bring forward several factory innovations that ultimately led to the development of the moving assembly line.
On Oct. 7, 1913, Ford’s team rigged a rudimentary final assembly line at the Highland Park Assembly plant. Engineers constructed a crude system along an open space at the plant, complete with a winch and a rope stretched across the floor. On this day, 140 assemblers were stationed along a 150-foot line and they installed parts on the chassis as it was dragged across the floor by the winch. Man hours of final assembly dropped from more than 12 hours under the stationary assembly system to fewer than three. In January 1914, the rope was replaced by an endless chain.
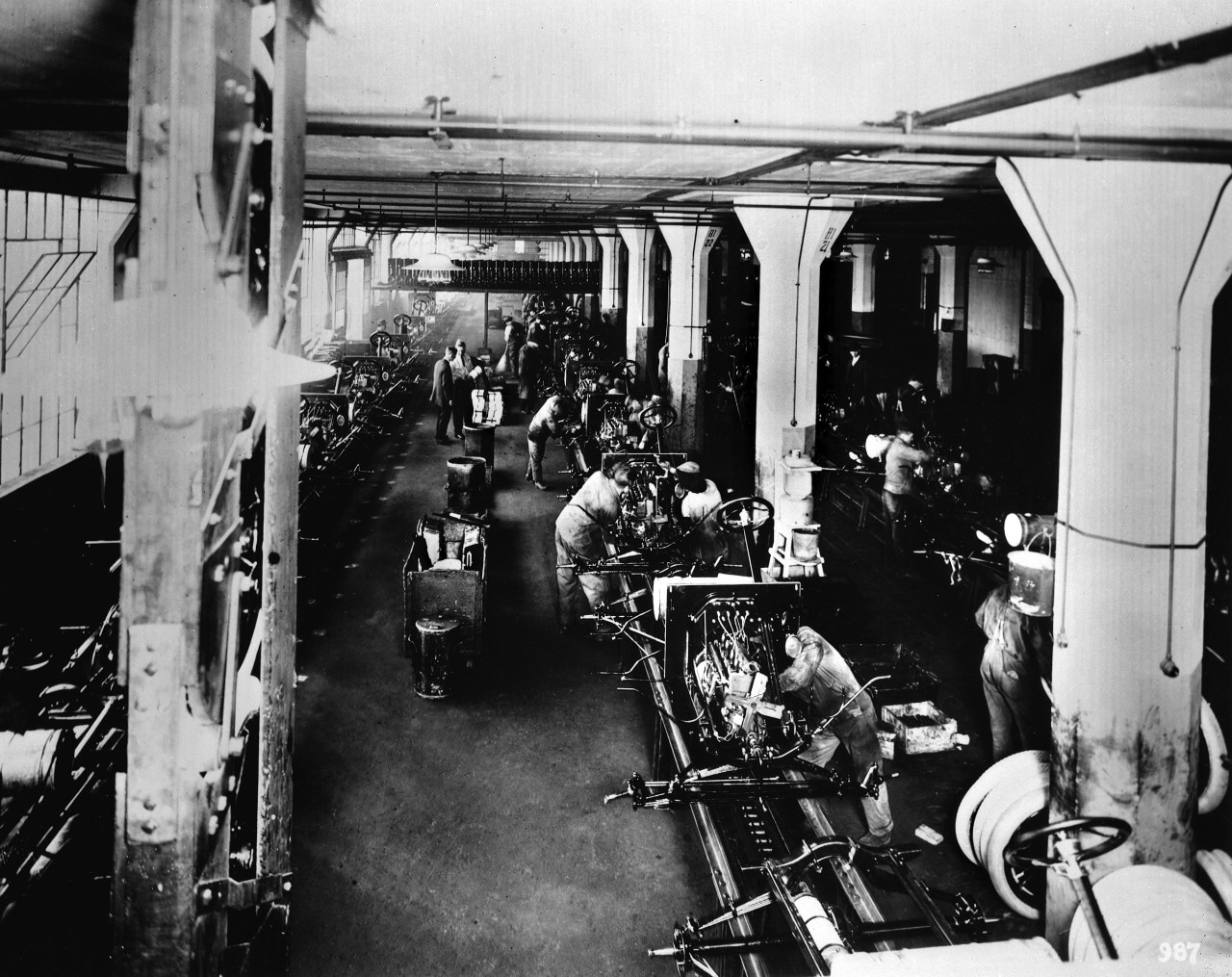
By bringing the work to the men, Ford engineers managed to smooth out differences in work pace. They slowed down the faster employees and forced slower ones to quicken their pace. The results of mass production were immediate and significant. In 1912, Ford Motor Company produced 82,388 Model Ts, and the touring car sold for $600. By 1916, Model T production had risen to 585,388, and the price had dropped to $360.
“Fordism” – large-scale production combined with high wages – was born and spread to other industries around the world. Soon, even small automobile companies producing only a few hundred cars per year were attempting to install moving assembly lines.